Understanding China Die Casting Molds: The Backbone of Metal Fabrication
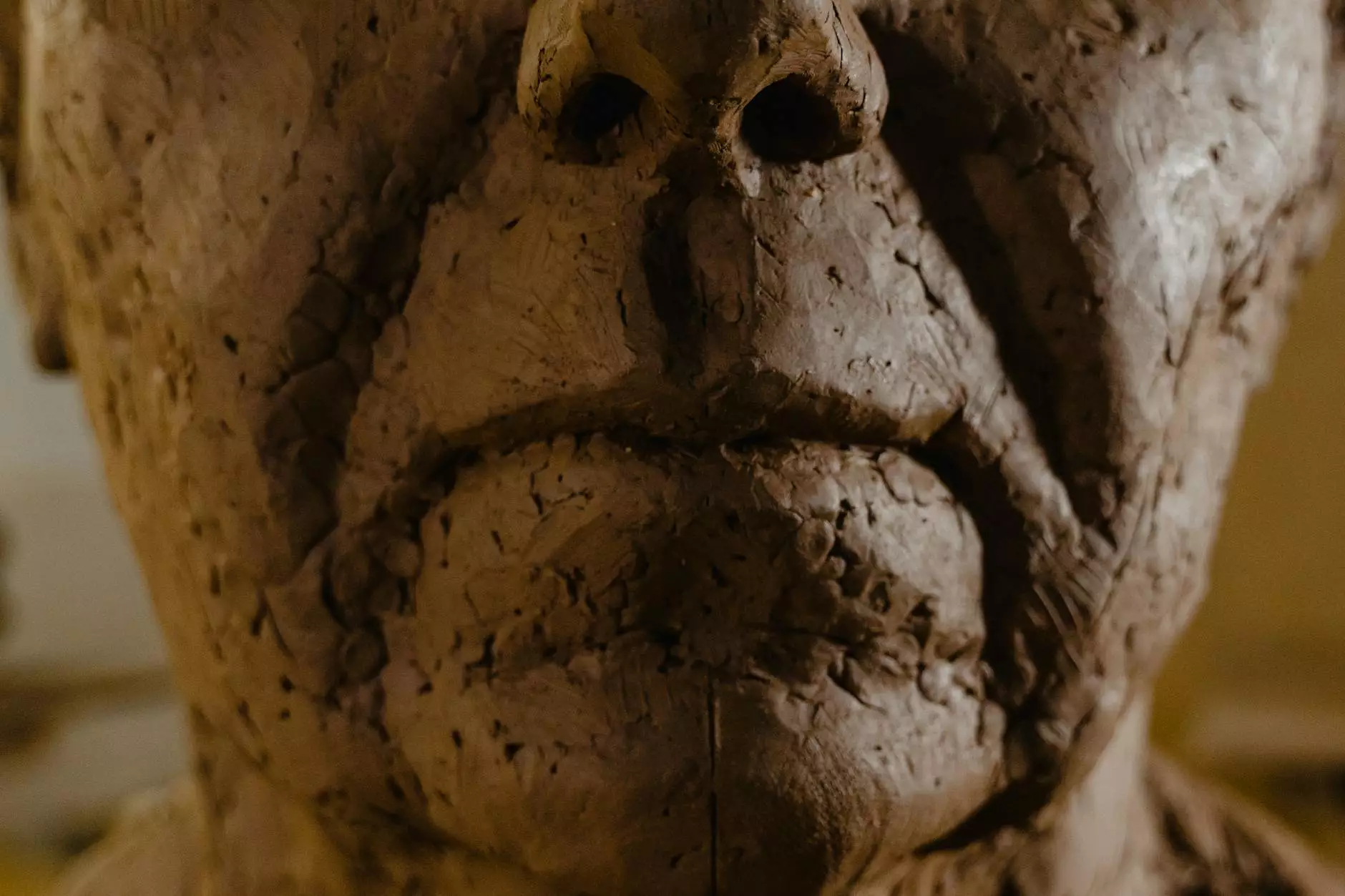
China die casting molds are a cornerstone of the manufacturing and metal fabrication industries. With the rapid development of technology and the increasing demand for high-quality precision parts, understanding the intricacies of die casting and the molds used in this process is crucial for manufacturers and businesses alike.
The Fundamentals of Die Casting
At its core, die casting is a manufacturing process that involves forcing molten metal into a mold under high pressure. The process is widely used for producing significant volumes of parts with intricate shapes and excellent surface finishes. Let's delve deeper into the components and stages involved in die casting:
Core Components of Die Casting
- Die Mold: The primary tool used to shape the metal.
- Melting Furnace: Where the metal is melted before the casting process.
- Injection System: This system injects the molten metal into the die.
- Cooling System: Responsible for cooling the part within the mold.
- Ejection System: Ejects the finished part from the mold once it has solidified.
Advantages of Using China Die Casting Molds
When it comes to die casting, China die casting molds represent a significant advantage for businesses due to several reasons:
1. Cost-Effectiveness
China is known for its competitive manufacturing pricing. By producing die casting molds in China, companies can reduce production costs significantly. This is particularly beneficial for those looking to scale their operations while maintaining quality.
2. High Precision and Quality
Manufacturers in China invest heavily in advanced technology and skilled labor. This results in die casting molds that are capable of producing highly precise parts that meet stringent international standards.
3. Versatility of Materials
The die casting process allows for a wide range of materials to be used. Common materials include:
- Aluminum
- Zinc
- Copper
- Magnesium
This versatility makes China die casting molds suitable for a variety of applications across multiple industries.
Applications of Die Casting in Various Industries
Die casting finds its application in many industries due to its flexibility and efficiency. Below are some key sectors leveraging die casting technologies:
1. Automotive Industry
The automotive industry is one of the largest consumers of die casting. Components such as engine blocks, transmission cases, and various structural parts are manufactured using die casting due to the strength and lightweight nature of the materials used.
2. Electronics Industry
With the rise of consumer electronics, die casting molds are frequently used to produce housings for devices like laptops, smartphones, and televisions. The precision and smooth finishes provide a high aesthetic value while maintaining functionality.
3. Aerospace Sector
In the aerospace sector, components made from die casting must meet rigorous safety and performance standards. Industries rely on China die casting molds to create lightweight but strong parts that contribute to fuel efficiency and safety.
Choosing the Right Die Casting Partner
Selecting a reliable die casting partner, especially within China, involves careful consideration. Here are key factors to evaluate:
1. Experience and Expertise
The industry experience of the casting manufacturer is paramount. A company with years of experience is likely to have refined processes and quality control measures.
2. Technological Capability
Look for manufacturers who use the latest technology in their casting processes. Advanced machinery can provide better precision and efficiency in producing molds.
3. Quality Certifications
Ensure the manufacturer holds recognized industry certifications such as ISO 9001, which reflects their commitment to quality management systems.
4. Communication Skills
Effective communication is crucial for a successful partnership. Ensure the manufacturer can clearly articulate processes, timelines, and potential issues.
Future Trends in Die Casting Technology
The die casting industry is evolving, and several trends suggest how the future may look:
1. Automation and Robotics
Integrating automation and robotic systems into die casting processes will increase efficiency and reduce human error. This shift will lead to faster production rates and consistent quality.
2. Sustainable Practices
As environmental concerns grow, manufacturers are increasingly focusing on sustainable practices, such as reducing waste during the die casting process and implementing recycling programs for scrap material.
3. Development of New Alloys
The exploration of new metal alloys designed specifically for die casting can yield lighter and stronger components, pushing the boundaries of what is achievable in various applications.
Conclusion: The Importance of Die Casting Molds
In conclusion, China die casting molds play an essential role in modern manufacturing across numerous industries. Their ability to produce high-quality, precise, and cost-effective parts cannot be overstated. Companies like DeepMould.net are at the forefront of this industry, providing reliable and innovative solutions to meet the ever-increasing demands for quality and efficiency in metal fabrication. By understanding the benefits and applications of these molds, businesses can make informed decisions that enhance their production capabilities and competitiveness in the market.
As you consider the future of your manufacturing processes, it's clear that embracing die casting and partnering with experienced suppliers will be key to achieving success in today's dynamic industry landscape.