High Pressure Die Casting Tooling: A Comprehensive Overview
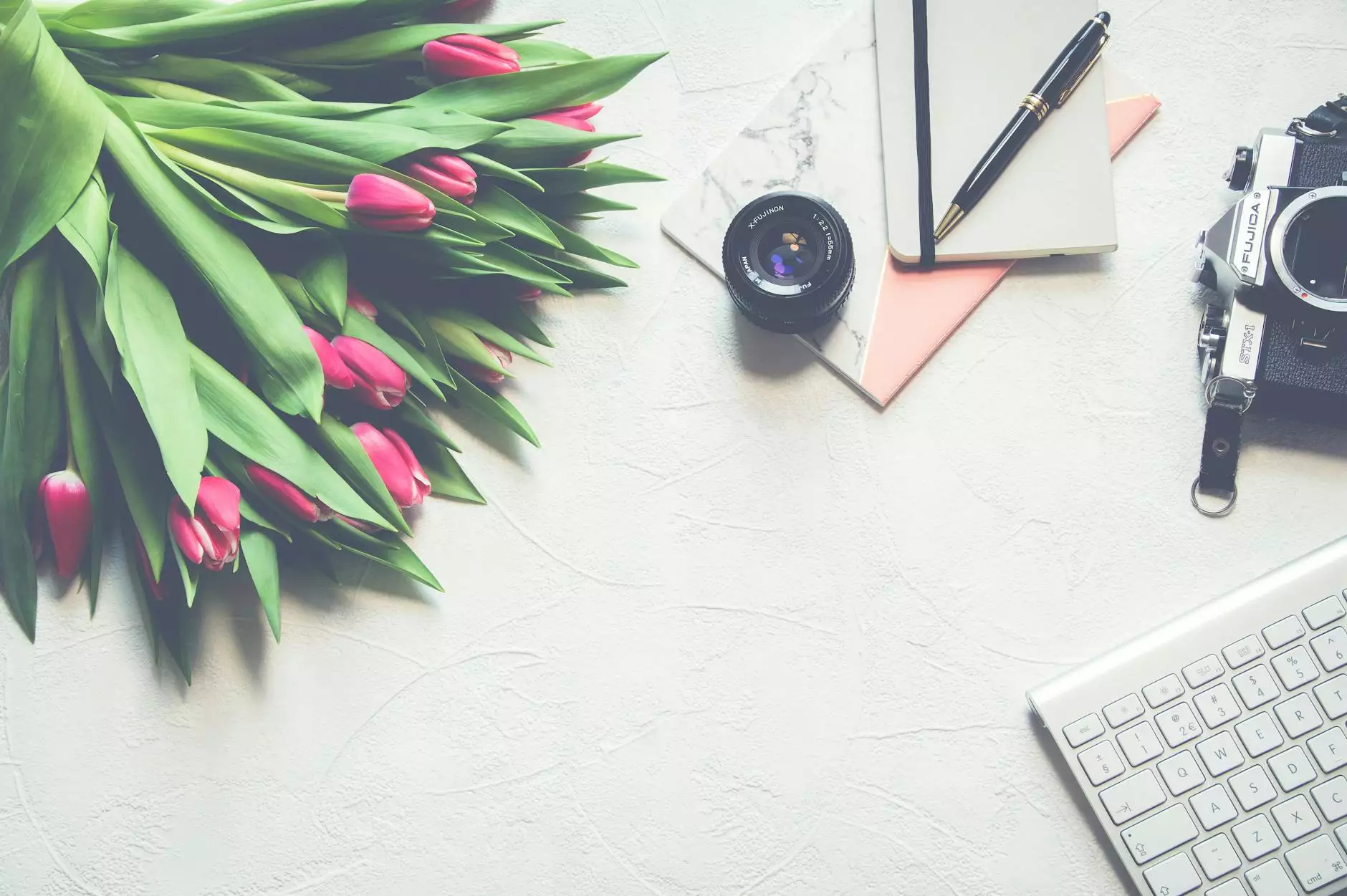
In today's robust manufacturing landscape, high pressure die casting tooling stands out as a critical technology within the realm of metal fabrication. This article delves into the intricacies of this process, highlighting its benefits, applications, and the innovations at the forefront of this industry.
What is High Pressure Die Casting?
High pressure die casting is a manufacturing process used for producing metal parts by forcing molten metal into a mold cavity under high pressure. This technique allows for quick production rates of complex shapes with excellent surface finishes, making it a popular choice for various industries. The process is particularly beneficial for producing small to medium-sized parts with high dimensional accuracy.
The Process of High Pressure Die Casting
The high pressure die casting process can be broken down into several distinct stages:
- Mold Preparation: The mold is pre-treated to ensure proper release of the finished part.
- Melting Metal: Metal is melted in a furnace and kept at a specific temperature before it is transferred to the die casting machine.
- Injection: Molten metal is injected into the mold at high pressure, which allows it to fill the cavity quickly and uniformly.
- Cooling and Solidification: The metal cools and solidifies in the mold to form the desired shape.
- Demolding: Once solidified, the mold opens, and the finished part is ejected.
- Finishing Operations: After demolding, further operations like trimming, machining, or surface treatment may be performed to refine the part.
Advantages of High Pressure Die Casting Tooling
Utilizing high pressure die casting tooling offers numerous benefits that enhance production efficiency and quality. Here are some key advantages:
- Precision and Complexity: High pressure die casting allows for intricate designs and tight tolerances, which are difficult to achieve with other manufacturing methods.
- Material Savings: The process minimizes waste, as excess material can be re-melted and reused, making it environmentally friendly.
- High Production Volume: The speed of the process means that high quantities of parts can be produced in a short period, making it cost-effective for large runs.
- Superior Surface Finish: The process often results in superior surface finishes, reducing the need for additional finishing work.
- Versatile Material Options: High pressure die casting can accommodate a range of materials, including aluminum, zinc, and magnesium alloys.
Applications of High Pressure Die Casting
The applications of high pressure die casting tooling are vast and diverse. Industries that commonly use this technology include:
- Automotive: Engine blocks, transmission cases, and other critical components are often cast using this method.
- Aerospace: Lightweight and strong components for aircraft require precision manufacturing that high pressure die casting provides.
- Consumer Electronics: Housings for mobile devices and laptops are produced using high-pressure die casting to ensure durability and aesthetics.
- Industrial Machinery: Parts for various equipment and machinery are routinely produced using this effective technique.
The Technology Behind High Pressure Die Casting Tooling
Understanding the technology that drives high pressure die casting tooling is essential for stakeholders in the metal fabrication industry. Key technological advancements include:
- Computer-Aided Design (CAD): Sophisticated modeling software allows for precise designs and simulations, aiding in the mold creation process.
- Advanced Material Research: Innovations in metal alloys enhance performance and reduce weight, broadening the application range.
- Automation: Modern die casting machines are increasingly automated, improving precision and reducing labor costs.
- Quality Control Technologies: Non-destructive testing and real-time monitoring systems ensure that only parts meeting strict quality standards are produced.
Cost Considerations in High Pressure Die Casting
While high pressure die casting tooling offers numerous advantages, it is crucial to consider the associated costs and factors that can affect these costs:
Initial investment in molds and machinery can be substantial, but this is offset by the long-term savings offered by higher production efficiencies. Additionally, the cost of raw materials, labor, and maintenance of equipment must be factored into the overall budget. Over time, as more parts are produced, the initial investment can lead to significant savings, especially when producing large volumes.
Future Trends in High Pressure Die Casting
The future of high pressure die casting tooling is promising, with several trends expected to shape the industry:
- Increased Automation: The move towards greater automation will enhance efficiency and reduce production costs.
- 3D Printing for Tooling: Utilizing 3D printing technology to produce die casting molds can reduce lead times and increase design flexibility.
- Sustainability Initiatives: There is a growing emphasis on sustainable practices, including the use of recycled materials and energy-efficient processes.
- Development of New Alloys: Research into new metal alloys tailored for die casting applications will continue to expand possibilities.
Choosing the Right Partner for High Pressure Die Casting Tooling
When selecting a manufacturer for high pressure die casting tooling, it is essential to consider the following criteria:
- Experience: Look for a provider with a proven track record in high pressure die casting.
- Technological Capabilities: Ensure they utilize the latest technology and machinery to meet your specifications.
- Quality Assurance: Assess their commitment to quality control and assurance practices.
- Customization: A good partner should offer tailored solutions to meet your specific needs.
DeepMould: Leading the Way in High Pressure Die Casting Tooling
DeepMould is at the forefront of high pressure die casting tooling, providing unparalleled solutions for various industries. With expertise in metal fabrication, DeepMould employs state-of-the-art technology and highly skilled artisans to deliver high-quality products that meet exacting standards.
Our Commitment to Quality
At DeepMould, our commitment to quality is reflected in every project we undertake. We ensure that our tooling meets rigorous specifications through comprehensive testing and quality assurance measures. This focus on quality not only enhances the durability of finished products but also satisfies our clients' diverse requirements.
Client-Centric Approach
We pride ourselves on our client-centric approach, ensuring that we understand the unique needs of our customers. Our team works closely with clients from initial consultation through to final delivery, making adjustments to designs and processes as necessary to ensure complete satisfaction. This level of collaboration ensures that we provide exceptional value in every project.
Innovative Solutions
Our investment in research and development allows DeepMould to offer innovative solutions in high pressure die casting tooling. We continually explore new materials, processes, and technologies that enhance efficiency and reduce costs, ultimately benefiting our clients.
Conclusion
In summary, high pressure die casting tooling is a vital component in metal fabrication, delivering precision, efficiency, and cost-effectiveness across various industries. With the ongoing advancements in technology and the emphasis on sustainability, this process is set to grow in prominence.
Choosing an experienced and innovative partner like DeepMould ensures that your manufacturing needs are met with the highest standards of quality and efficiency. As the industry continues to evolve, staying informed about trends and advancements will help businesses remain competitive in this dynamic landscape.
Learn more about our high pressure die casting solutions at deepmould.net.